Pressure sensitive adhesion for solar
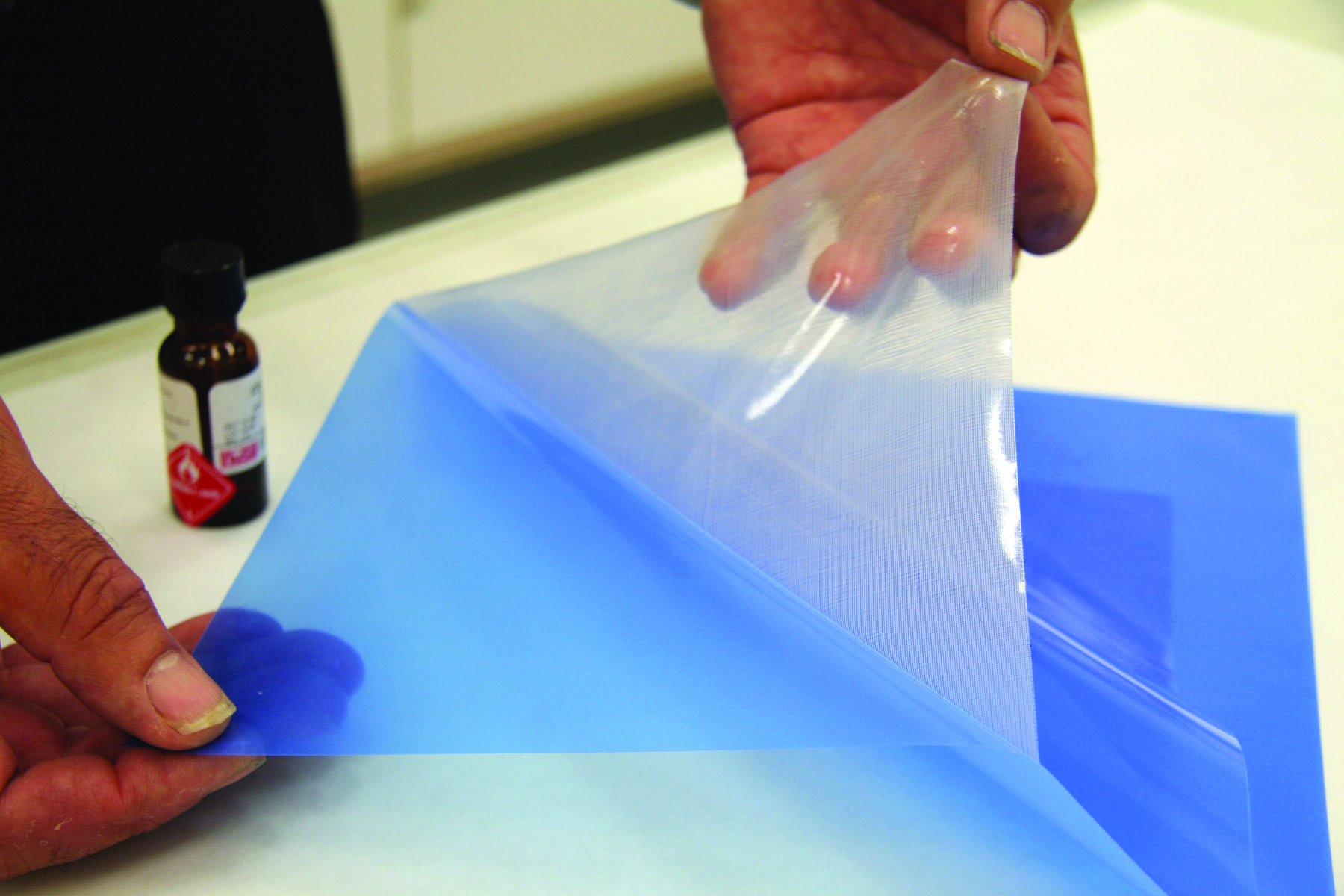
Through the thickness of a PSA or film, the bond line thickness between the cell and the cover glass can be controlled, facilitating solar cell assembly. Also, design engineers have the ability to rework panels where PSAs are applied "“ cutting cost for components and time. Low outgassing PSAs and film adhesives also have similar performance to liquid silicone adhesives, specifically good chemical stability, broad operating temperature ranges, low modulus during thermal cycling, and minimal or no mixing and de-airing. With dimethyl backbone chemistries similar to traditional adhesives, the clear PSAs and thin films are resistant to yellowing and have light transmittance greater than 97% at 400 nm.
Pressure sensitive adhesive film
Two part, mixable silicone adhesives are widely used in the space power arrays as adhesives for cover glasses and bonding solar cells to substrates. A possible alternative for these adhesives may be space-grade pressure sensitive adhesives (PSA) films or, if a fully cross-linked adhesive with a very strong bond is necessary, a curable film adhesive. These materials can be handled as semi-cured films, offering quick adhesion with no mess, and can be die-cut to specific shapes prior to application. These are some of the advantages of PSAs and curable film adhesives over liquid adhesives.
Silicone PSAs are made by partially crosslinking a silicone polymer with a silicone resin, forming a loosely knit elastomer. The PSA adhesion works by hydrogen bonding to surfaces; hydrogen bonds are polar, intermolecular forces that although fairly weak can offer excellent adhesion in large quantities. The hydrogen bonding adhesion is typically low at initial contact but improves significantly as the PSA wets onto the substrate. The initial adhesion is called tack and is quantified as the force required to remove a probe quickly touched to the adhesive film.1 The wetted-out adhesion is typically measured by a peel or lap shear test, usually after 24 hours.2
Controlled Volatility (CV) PSAs, suitable for use in space environments, can be made by removing most of the low molecular weight species of a typical silicone PSA. The volatility can be lowered to surpass the ASTM E595 Controlled Volatility testing specification of 1.0% Total Mass Loss (TML) and 0.1% Controlled Volatility Condensable Material (CVCM). The PSA is initially in solvent and can be coated onto different substrates or can be delivered coated directly onto a release liner to make a free film. Silicone PSAs can be supplied at a thickness from 25 "“ 125 micron (1 mil to 5 mil) in sheet or roll form, and the films can be die-cut to shape and applied like an ordinary tape. These PSAs have bond strengths ranging from 0.17 - 3.5 N/cm (0.1- 2.0 lb./in), tested using a 180° peel test.2
For peel testing, a PSA film is bonded to a 2.5 mm wide by 20 cm long (1 in x 8 in) aluminium substrate. The aluminium substrate is lightly sanded with 400 mesh sandpaper, cleaned with isopropyl alcohol and permitted to dry 30 minutes. The release liner is removed from one side of the PSA and pressed down onto the aluminium substrate in an air-free manner. A 2.27 kg (5-lb) weight is rolled over the bonded PSA sample once and the sample is permitted to rest period at ambient temperature for 24 hours prior to testing.
Adhesion can develop in minutes; but, typically, adhesion improves over time as the adhesive wets over the surface. Adhesion can be formulated from low tack, or low adhesion, for temporary bonds that can later be easily removed, or from a higher tack PSA with good adhesion of approximately
3.5 N/cm (2 lb./in) for more permanent bonds.
Figure 1 shows a 180° peel test being performed. The PSA coated Kapton tape is held in the upper clamp of the MTS while the aluminium panel is held in the lower clamp. The crosshead moves up and peels the tape off of the aluminium panel.
Figure 2 illustrates the results of a typical peel test. The PSA coated Kapton tape is pulled off of the aluminium substrate and the force is recorded. In Figure 2, the y-axis is linear stress (lb./in), and crosshead travel is on the x-axis. A peel test consists of peeling a minimum of 20 cm (8 in) of the PSA off of the aluminium substrate, and then the average force between 2.5 cm (1 in) and 18 cm (7 in) of travel is reported for the peel.
Many PSAs have poor adhesion at extreme temperatures. At high temperatures, some PSAs will melt or soften, and the adhesive strength fails. A solution to this problem is to partially crosslink the PSA so it has good high-temperature adhesion. Silicone PSAs also offer advantages at low temperatures; their low glass transition temperatures (Tg) permit them to remain flexible at low temperatures.
CV PSA samples were prepared on aluminium and stainless steel panels and tested for peel strength at -55°C (-67°F) and 150°C (302°F). PSA coated Kapton tapes were bonded to the metal substrates, a 2.2 kg (5 lb.) weighted roller was rolled over the samples, and the samples were permitted to sit 24 hours at room temperature before 180° peel testing. The results are presented in Table 1. Figures 3 and 4 are the actual results of the stainless steel peel testing.
While most two-part, fully cross-linked silicone elastomers offer good adhesion at elevated temperature, many PSAs do not. A relatively simple pass/fail test to measure the heat resistance of the PSA bond is a static shear test. The test was designed to evaluate the shear strength of a PSA to support a mass at 175°C, 25°C hotter than the typical satellite bake-out temperature.
Figure 5 illustrates a static shear test. For the static shear test, a sample is prepared by bonding 6.5 sq. cm (1 sq. inch) of adhesive to an aluminium panel. The sample has a rest period of 24 hours. The panel is then suspended in an oven, and a 50 g weight is hung on the panel while the oven is heated to 175°C. The PSA is required to remain bonded to the aluminium panel for 24 hours without falling off the suspended aluminium panel.3
Silicones typically have a low glass transition temperature (Tg), the point at which a material goes from a rubbery elastomer to a glassy solid, and the CV PSA is similar in this respect. Below (Figure 6) is a graph of the modulus of the PSA as it is heated from -140ºC, using Dynamic Mechanical Analysis (DMA). The rate of heating was 5°C/min, the frequency was 1 Hz and the amplitude was 1 um. A film tensile clamp held the sample during testing. The PSA has peak tan delta of -116°C (-177°F), which is typically reported as the glass transition temperature. E' onset, the storage modulus, occurs around -125°C (-193°F) and is associated with mechanical failure. E" peak, the loss modulus, is recorded at -122°C (-198°F). These values are typical for a dimethyl silicone.
Many two-part curable silicone elastomers are used as cover glass adhesives. These adhesives are required to be very clear, with > 95% transmittance through the visible light region. These adhesives are typically two-part, low viscosity adhesives that require more than 8 hours to cure. The assembled part cannot be handled until the silicone has partially cured.
PSAs offer an alternative to these types of adhesives. The PSA offers instant tack, and the parts can be handled almost immediately after bonding. As a cover glass adhesive, the PSA offers good light transmittance from 375 nm to 1,100 nm. The PSA itself is very clear, wets out on practically any surface and offers good optical coupling between substrates. The refractive index of the PSA is 1.41.
Figure 7 is a UV/Vis graph of the transmittance of light through the PSA.4 The PSA was sandwiched between two glass microscope slides, and a glass microscope slide was used as a blank.The PSA films can be die-cut to form shapes, or sheets of PSA can be cut to multiple shapes. These films can then be transferred to large areas and are then ready for the next substrate to be applied, e.g. cover glasses. One disadvantage of PSAs is the difficulty of handling such relatively thin films because they easily tear. Films, especially the thinner films, should be transferred from a release liner to a substrate and not handled as film. In addition, as the films are sticky, they are difficult to keep from adhering to themselves.
Also, the transfer from release liner to substrate is critical so no bubbles or flaws are introduced. Bonding two flat, rigid pieces can present some difficulties. While flexible pieces can be rolled down onto the PSA, minimizing bubble entrapment, rigid pieces almost always capture a bubble and must be vacuum-bagged for a period of time to remove the air bubbles. This sometimes introduces a wrinkle in the PSA film. Fortunately, all of these problems have been solved in production, for example, by automakers sandwiching a plastic liner between sheets of windshield glass.
PSAs are silicones so the Coefficient of Thermal Expansion (CTE) is relatively high at approximately 300 ppm/ºC but the modulus of the PSA film is quite low so the films have some "give" between substrates of different CTE during thermal cycling not unlike the typical liquid silicone adhesives currently in use.
CV grade film adhesive
Two-part curable films are different than PSAs. PSAs are pre-cured and offer moderate adhesion without any further cure. A two-part system is similar to the current liquid silicone adhesives except that Part A is a semi-solid film and Part B is a liquid activator similar to a primer. The adhesive is applied by wiping the liquid Part B onto a surface, permitting the solvent to evaporate for 15 minutes, applying the Part A film adhesive, and then pressing the two substrates to be bonded together. The adhesive can be heat accelerated at 60°C for 4 hours or permitted to cure for 24 hours at room temperature. Humidity is not a factor for the cure. Typically Part A, the film adhesive, is made in thicknesses ranging from 0.18 "“ 0.76 (7 mils to 30 mils). These films can be filled with thermally conductive fillers, electrically dissipative fillers, or both.
The films come on release liners and can be handled as free film transferred from the release liner to a substrate and then bonded to a catalysed substrate. If uncatalyzed, they have practically unlimited shelf life and will cure after catalyzation at room temperature in 24 hours or can be heat-accelerated. The film is a firm, uncured silicone that can be handled, die-cut, or pressed onto substrates and still maintain its dimensions. When cured, it is a fully cured silicone elastomer with adhesion properties similar to liquid adhesives.
Some disadvantages of the low viscosity adhesives typically used to bond solar cells are carefully mixing, de-airing, and applying a measured film of the adhesive onto a substrate to which the solar cells are bonded. The film adhesive offers a controlled bondline, the adhesive requires no mixing, and the film adhesive offers enough tack so the substrates can be handled immediately after bonding.
A typical test for a solar cell adhesive is a lap shear, meaning the adhesive is cured between two panels, and the panels are then pulled apart on a tensile tester to measure the force required to pull the two panels apart.5 A 2.5 cm square portion of the lap shear panel is covered with adhesive and another panel is laid on the adhesive with the unbonded portions facing away from each other.
The film adhesives are tested for lap shear strength. The films are bonded at 6.5 cm2 (1 in2 ), cured at 60°C and pulled apart at 0.02cm/min (0.05"/min) on a tensile tester. The resulting lap shear should be greater than 1.4 mPa (200 psi).
Figure 9 depicts a typical test result for a two-part, unfilled film adhesive.
Another bonding difficulty on solar cell assemblies is bonding the through-wires on the back of a solar panel. The electricity from the solar cells is collected and eventually the wires need to go through the array substrate; all the individual wires are combined and then combined again into a large cable. All the individual wires are tacked down on the back of the solar array substrate.
Currently, a two-part, mixable silicone is used. The area around the wirers is masked to prevent any contamination, the wires are held in place, and the adhesive is applied. The adhesive may need to be applied two times to build up enough thickness to hold the wire. The wires still need to be held in place while the silicone cures. Calendered films can be cut into tapes suitable for tacking wires down, the activator is wiped on the solar array substrate permitted to dry; then the film adhesive is pressed down over the wires, and in 8 hours the adhesive is cured.
Figure 10 illustrates how cured film adhesives can be used to tack down wires on a composite board. The Part B activator was applied to the board (the slightly dark areas around the adhesive strips). The film adhesive was pressed down through the wire and, again, the Part B activator was applied to the surface of the film adhesive. The adhesive was cured in approximately 8 hours. The translucent adhesive is an unfilled CV silicone reinforced with fiberglass scrim. The black tape is an electrically dissipative material. Fillers can be added to the Part A films for different properties such as thermal conductivity. They can be filled with non-electrically conducting ceramic fillers like aluminium oxide or zinc oxide and have thermal conductivities of up to 1 W/mK. These films are white and are similar to the unfilled films.
In addition, carbon black can be added to the silicone films to offer electrical conductivity. The electrically dissipative films can have resistivities from 108 ohm-cm to 400 ohm-cm.6 Films can be developed with other fillers to tailor properties as desired.
Conclusions
Silicone PSAs are different from curable film adhesives; PSAs are semi-cured films that provide adhesion through hydrogen bonding and have immediate tack while adhesion builds up over a longer time, around 24 hours. The adhesion is typically from 1.0 - 3.5 N/cm (1 - 2 lb./in) for peel testing. PSA film thickness usually runs from 25 "“ 75 microns (0.001" to 0.003"). PSAs are optically clear.
Silicone film adhesives offer an alternative to two-part, mixable silicone elastomeric adhesives. Curable film adhesives are two-part systems that include a calendared sheet of Part A, typically 175 - 750 microns (0.007" to 0.030"). The Part B is applied as a liquid and evaporates in 15 minutes, and then the Part A film is applied. The silicone cures in 8 hours at room temperature. Both adhesives offer short cure times and pre-cut peel-and-stick operations for quick manufacture of parts with little to no wait time for the cure. The PSA bonds quickly enough to be handled immediately. Film adhesives offer permanent adhesion to a variety of substrates in a pre-formed, controlled thickness format. Both materials provide additional options for adhesive bonding in the manufacture of solar arrays.
In summary, new options are available as adhesives for spacecraft: silicone PSAs and two-part curable films. These films offer manufacturers increased flexibility and improved turnover rates with faster cure and ease of handling.
© 2013 Angel Business Communications.
Permission required.