Six metre long flexible solar module on display
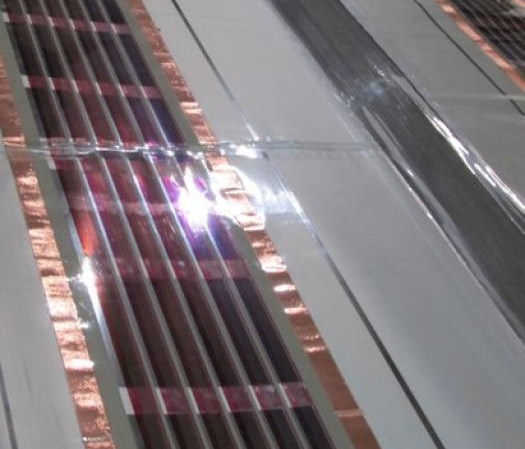
A solar module, six meters long and 50 cm wide, consisting of flexible organic solar cells is the result of the European research project "FabriGen," a joint effort between six partners from four different countries. This novel power producing foil will be on display at an upcoming conference.
. The module is manufactured exclusively with a roll-to-roll process. The organic solar cells do not contain the customary indium-tin-oxide and therefore have the potential to be particularly economical. The project idea targeted applications in the field of membrane architecture, which incorporates tensile membrane structures as roofs, for example, in the architectural design.
"FabriGen, fabric structures for solar power generation" is an EU-sponsored project. Its project partners from Germany, Great Britain, the Czech Republic and Bulgaria had the mutual goal of developing fabric structures which are integrated with organic solar cells.
The project was initiated by Robert Carpenter, Managing Director of Inside2Outside (I2O), a medium-sized company in Great Britain. For his special fabric structures with organic solar cells, he has a variety of different uses in mind, especially in the field of architecture.
Applications include shading systems for pedestrian zones and bus stops as well as shed and carport roofs. The focus lies in cost-effectively covering large areas with flexible polymer constructions which cost markedly less than glass. By making use of complex structures through membrane design, the area in question can be made as large as possible, thus maximizing the solar gain. At the same time, transport and installation costs are kept low due to the light weight of the structure.
"We are pleased to have produced this successful prototype with our partners within the short time span of six months," says Dr. Birger Zimmermann, Team Leader of Production Technology for Organic Solar Cells at Fraunhofer ISE.
"Manufacturing the textile structure equipped with organic photovoltaic modules was a real joint effort," remembers the project coordinator Robert Carpenter, I2O. "From vacuum processing the metal electrode at CPI, followed by coating the organic semiconductor at Fraunhofer ISE through to printing the silver contacts and the lamination at Coatema and lastly the high frequency welding of the solar foil on the fabric membrane at I2O, a range of expertise was involved."
The solar cell structure and the module design were developed at Fraunhofer ISE. The Freiburg researchers were also involved in the encapsulation development under the leadership of CPI in Great Britain. All project partners contributed their input to integrating the photovoltaics into a fabric membrane, above all, CPI and the project coordinator Inside2Outside Ltd. Coatema Coating Machinery GmbH was responsible for the process development of the large area lamination.