News Article
Solar panels faster acoustic inspection
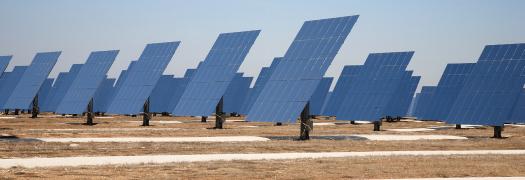
By maximizing the scan area and developing innovative software, it is possible to significantly increased both the speed and the efficiency of the inspection process. Tom Adams, consultant, at Sonoscan, Inc explains.
The structural defects that solar panels are inspected for include cracks in the silicon, delaminations between the silicon and the silicone adhesive, delaminations, broken traces, and others. Any of these structural defects can diminish the performance and lifespan of a solar panel.

Some of the most critical and most frequent structural defects involve the solder that joins the bus bar to the silicon cells. These defects include non-bonds or partial bonds (which may be caused by surface contamination on the silicon) between the solder and the cell, as well as voids (air bubbles) in the solder. The defects may have all sorts of configurations, but are undesirable because they shrink the area of contact between the cell and the bus bar, and because physical and thermal stresses during service are likely to shrink the area of contact even more. Eventually the contact is broken. In the best case, only the single cell is lost; in the worst case, the entire panel goes dead. These structural defects are not visible optically but are easily seen by acoustic micro imaging tools. They are typically too thin to be imaged by x-ray.
Ideally a solar panel will go into service and operate with high efficiency for its expected lifetime. Structural defects involving the solder joints can seriously compromise this performance. A cold joint, where the solder is in place but not bonded at all to the solar cell, may be intermittent and may or may not be detected by electrical testing. But when a solder joint is only partly bonded or harbors voids, the bus bar can lose contact with the solar cell gradually until it abruptly fails. In order to eliminate problem solder bonds, a manufacturer can perform acoustic imaging of the panel during assembly. Rework can often be performed to ensure normal operation in service.
Countless devices, modules and assemblies aside from solar panels run the risk of sudden field failure caused by loss of electrical contact between two elements. Most of these items are smaller than a solar panel in their x-y dimensions, and fit nicely onto the scanning stage of most acoustic micro imaging (AMI) tools. The defects in solar panels, and particularly in bus bar solder joints, are similar to the defects in smaller devices, but the solar panel itself is far larger. Using a standard AMI system it is possible, but unwieldy and time-consuming, to examine all of the bus bar connections in a solar panel. Typically the operator will position the panel and the ultrasonic transducer will scan one small area to produce an acoustic image. The operator will then reposition the panel to scan the next small area, and so on until the entire area of the panel has been scanned. This method is effective but tedious.
Sonoscan also developed a C-SAM AMI tool that has a much larger scan area (0.6096 m x 0.6096 m) than other laboratory, semi-automated or automated AMI tools. It is shown scanning the bottom side of a large pc board (solar panels being proprietary) in Figure 1. Some solar panels can be imaged in their entirety in one scan, without repositioning the panel. Even panels measuring up to 1m x 3m require relatively few scans. Because there are many fewer interruptions of the scanning process to reposition the solar panel, inspection is much faster. To further speed the inspection process, Sonoscan has developed software that can accommodate scanning to the geometry of the panel. The layered structure of the panel may have defects such as cracks or delaminations in the silicon and other materials, but such defects are both less common than and less lethal than bus bar defects. The new software therefore scans only the bus bars, looking for anomalies and defects in the bonds between the bus bar and cells. This selectivity greatly reduces scan time and the area that must be scanned, and means that even very large solar panels can be inspected for the most dangerous features in the shortest possible time.
The concept of scanning only the most relevant regions of a sample is used by Sonoscan in non-solar applications as well. An AMI system having a smaller scan area, for example, may be scanning a JEDEC-style tray that contains only a few large parts. Time may be saved if each of the few parts is scanned individually, without scanning the regions of the tray that contain no parts. The two major types of solar cells are both imaged acoustically in panel form, but not at the same stage of production. Thin film solar cell panels have no backside material that will block the transmission of ultrasound, and the common anomalies and defects occur on the backside. Thin film panels are typically imaged just after busing.
Traditional glass solar cell panels differ in that a strengthening material is placed on the backside of the panel. The material covers the whole area of the backside and prevents ultrasound from reaching and imaging the solar cells. A reflective coating makes imaging from the frontside impractical. For these reasons, traditional panels are imaged from the back side just before the strengthening material is applied.
During the acoustic imaging process, the AMI tool's transducer is coupled to the panel's surface by a column of water that rides with the transducer. The transducer scans across the width of the bus bar at a given point, moves fractionally, and scans back across the bus bar. The transducer moves back and forth across the bus bar at relatively high speed. Thousands of times a second, it sends a pulse of ultrasound into the panel and receives return echoes having various amplitudes. The transducer typically has a long focal length and pulses 230 MHz ultrasound to achieve the highest spatial resolution in the acoustic images.
Well bonded material interfaces in the bus bar attachment reflect a portion of the ultrasound; another portion crosses the interface and travels deeper into the sample. A well bonded bus bar will therefore send back moderate-amplitude echoes that will appear gray in a monochromatic acoustic image. But any material gap, even if it is as thin as 100à…, will send back a maximum-amplitude echo that will be displayed as bright white in the acoustic image (Figure 2). The near-total reflection of the pulsed ultrasound is caused by the interface between a solid material and the air or another gas in the gap. Bright white features in acoustic image of the bus bars are non-bonds, voids, delaminations or other types of gaps. Their location and size are evaluated to determine how great a threat they pose to long-term performance.

Figure 3 is the acoustic image of one junction box, where the bus bar is soldered to the solar cell. The depth imaged was the glass-to-silicon interface. Imaging revealed two areas of concern:

Figure 3 is representative of the sorts of defects that need to be found during acoustic inspection of solar panels. By maximizing the scan area and developing innovative software, Sonoscan has significantly increased both the speed and the efficiency of the inspection process.

Some of the most critical and most frequent structural defects involve the solder that joins the bus bar to the silicon cells. These defects include non-bonds or partial bonds (which may be caused by surface contamination on the silicon) between the solder and the cell, as well as voids (air bubbles) in the solder. The defects may have all sorts of configurations, but are undesirable because they shrink the area of contact between the cell and the bus bar, and because physical and thermal stresses during service are likely to shrink the area of contact even more. Eventually the contact is broken. In the best case, only the single cell is lost; in the worst case, the entire panel goes dead. These structural defects are not visible optically but are easily seen by acoustic micro imaging tools. They are typically too thin to be imaged by x-ray.
Ideally a solar panel will go into service and operate with high efficiency for its expected lifetime. Structural defects involving the solder joints can seriously compromise this performance. A cold joint, where the solder is in place but not bonded at all to the solar cell, may be intermittent and may or may not be detected by electrical testing. But when a solder joint is only partly bonded or harbors voids, the bus bar can lose contact with the solar cell gradually until it abruptly fails. In order to eliminate problem solder bonds, a manufacturer can perform acoustic imaging of the panel during assembly. Rework can often be performed to ensure normal operation in service.
Countless devices, modules and assemblies aside from solar panels run the risk of sudden field failure caused by loss of electrical contact between two elements. Most of these items are smaller than a solar panel in their x-y dimensions, and fit nicely onto the scanning stage of most acoustic micro imaging (AMI) tools. The defects in solar panels, and particularly in bus bar solder joints, are similar to the defects in smaller devices, but the solar panel itself is far larger. Using a standard AMI system it is possible, but unwieldy and time-consuming, to examine all of the bus bar connections in a solar panel. Typically the operator will position the panel and the ultrasonic transducer will scan one small area to produce an acoustic image. The operator will then reposition the panel to scan the next small area, and so on until the entire area of the panel has been scanned. This method is effective but tedious.
Sonoscan also developed a C-SAM AMI tool that has a much larger scan area (0.6096 m x 0.6096 m) than other laboratory, semi-automated or automated AMI tools. It is shown scanning the bottom side of a large pc board (solar panels being proprietary) in Figure 1. Some solar panels can be imaged in their entirety in one scan, without repositioning the panel. Even panels measuring up to 1m x 3m require relatively few scans. Because there are many fewer interruptions of the scanning process to reposition the solar panel, inspection is much faster. To further speed the inspection process, Sonoscan has developed software that can accommodate scanning to the geometry of the panel. The layered structure of the panel may have defects such as cracks or delaminations in the silicon and other materials, but such defects are both less common than and less lethal than bus bar defects. The new software therefore scans only the bus bars, looking for anomalies and defects in the bonds between the bus bar and cells. This selectivity greatly reduces scan time and the area that must be scanned, and means that even very large solar panels can be inspected for the most dangerous features in the shortest possible time.
The concept of scanning only the most relevant regions of a sample is used by Sonoscan in non-solar applications as well. An AMI system having a smaller scan area, for example, may be scanning a JEDEC-style tray that contains only a few large parts. Time may be saved if each of the few parts is scanned individually, without scanning the regions of the tray that contain no parts. The two major types of solar cells are both imaged acoustically in panel form, but not at the same stage of production. Thin film solar cell panels have no backside material that will block the transmission of ultrasound, and the common anomalies and defects occur on the backside. Thin film panels are typically imaged just after busing.
Traditional glass solar cell panels differ in that a strengthening material is placed on the backside of the panel. The material covers the whole area of the backside and prevents ultrasound from reaching and imaging the solar cells. A reflective coating makes imaging from the frontside impractical. For these reasons, traditional panels are imaged from the back side just before the strengthening material is applied.
During the acoustic imaging process, the AMI tool's transducer is coupled to the panel's surface by a column of water that rides with the transducer. The transducer scans across the width of the bus bar at a given point, moves fractionally, and scans back across the bus bar. The transducer moves back and forth across the bus bar at relatively high speed. Thousands of times a second, it sends a pulse of ultrasound into the panel and receives return echoes having various amplitudes. The transducer typically has a long focal length and pulses 230 MHz ultrasound to achieve the highest spatial resolution in the acoustic images.
Well bonded material interfaces in the bus bar attachment reflect a portion of the ultrasound; another portion crosses the interface and travels deeper into the sample. A well bonded bus bar will therefore send back moderate-amplitude echoes that will appear gray in a monochromatic acoustic image. But any material gap, even if it is as thin as 100à…, will send back a maximum-amplitude echo that will be displayed as bright white in the acoustic image (Figure 2). The near-total reflection of the pulsed ultrasound is caused by the interface between a solid material and the air or another gas in the gap. Bright white features in acoustic image of the bus bars are non-bonds, voids, delaminations or other types of gaps. Their location and size are evaluated to determine how great a threat they pose to long-term performance.

Figure 3 is the acoustic image of one junction box, where the bus bar is soldered to the solar cell. The depth imaged was the glass-to-silicon interface. Imaging revealed two areas of concern:

- The bond between the bus bar and the silicon. Only the right and left regions of the bus bar display the medium gray tone that is indicative of successful bonding. There are significant regions (blue arrows) whose white color indicates that they are delaminated or non-bonded. In the center of the bus bar weld only small regions are well bonded (the medium gray seen at the left and right extremities) and there are numerous small delaminations. These anomalies may be the result of thermal interaction between the bus bar and the bond pad during assembly.
- The bond pad. Most of the area of the oval bond pad seems to be well bonded (evenly gray), but the outer edges of the bond pad are white - delaminated or non-bonded. Although these regions are relatively small, they are likely to expand in area until the bond itself is compromised. The bond pad is also surrounded by small more or less circular features that are likely to be voids.
Figure 3 is representative of the sorts of defects that need to be found during acoustic inspection of solar panels. By maximizing the scan area and developing innovative software, Sonoscan has significantly increased both the speed and the efficiency of the inspection process.